John McGinnis thinks ordinary families would rather skip the airport and fly themselves. So he is trying to reinvent the personal airplane with the help of his father, son, and a rotating crew of about two dozen volunteers. Unlike small aircraft today—which can cost more than a house—McGinnis says Synergy could be cheaper, quieter, and, at more than 40 mpg, three times as fuel-efficient.
McGinnis, a 47-year-old composite manufacturer, flew his first airplane in second grade. Perplexed by the inefficiencies of personal aircraft, he taught himself aeronautical engineering and fluid dynamics over two decades. One day, while perusing scientific studies at a desk in his daughters’ bedroom, he read a NASA researcher’s paper challenging a classic aerodynamic drag equation. McGinnis could see the possibilities. “I came out of the girls’ bedroom ranting like a madman to my wife,” he says. “ ’Honey, you’re never going to believe this. I think I just solved a problem I’ve been working on since I was a little kid.'”
Synergy’s wings bend upward and into a box shape for minimum drag and maximum efficiency. The top half of each wing swoops behind the body to function as a tail while providing greater in-flight stability. The double-box tail design also makes gliding easier by counteracting tornado-like vortices at the wings’ tips. And instead of a front-mounted propeller, an impeller placed behind the bullet-shaped body quiets noise while adding thrust.
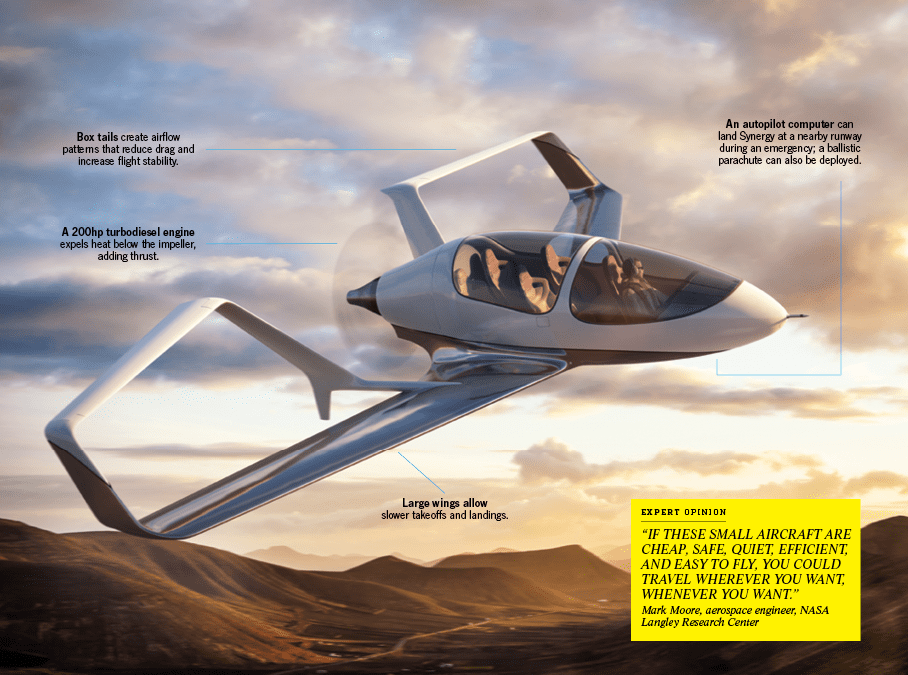
Synergy Illustration
1) A 200hp turbodiesel engine expels heat below the impeller, adding thrust.
2) Large wings allow slower takeoffs and landings.
3) Box tails create airflow patterns that reduce drag and increase flight stability.
4) An autopilot computer can land Synergy at a nearby runway during an emergency; a ballistic parachute can also be deployed.
![The McGinnis family—Pat, John, and Kyle—and pilot John Paul Noyes [front to back] stand in their Kalispell, Montana, workshop.](https://www.plazajournal.com/wp-content/uploads/2024/02/upload-3354.jpg)
Scale Models
McGinnis works on Synergy in his father’s garage, where he uses CNC machines and custom molds to fabricate components and 3-D software to rapidly model new ideas. Family members serve among the core build crew, with McGinnis’s son, Kyle, second-in-command. A quarter-scale prototype made from fiberglass, carbon fiber, and Kevlar suggests that both the team’s manufacturing process and unusual wing configuration work. Using about $80,000 in crowdfunded cash, they hope to finish a full-scale, five-person aircraft this year. “I work on it 90 hours a week, with a few hours of sleep,” McGinnis says. “What drives me to do it is that no one else will.”
INVENTOR
John McGinnis
COMPANY
Synergy Aircraft
INVENTION
Synergy
COST TO DEVELOP
Undisclosed
MATURITY
2/10
See the rest of the articles from our 2013 Invention Awards section here, and see all of our May issue here.