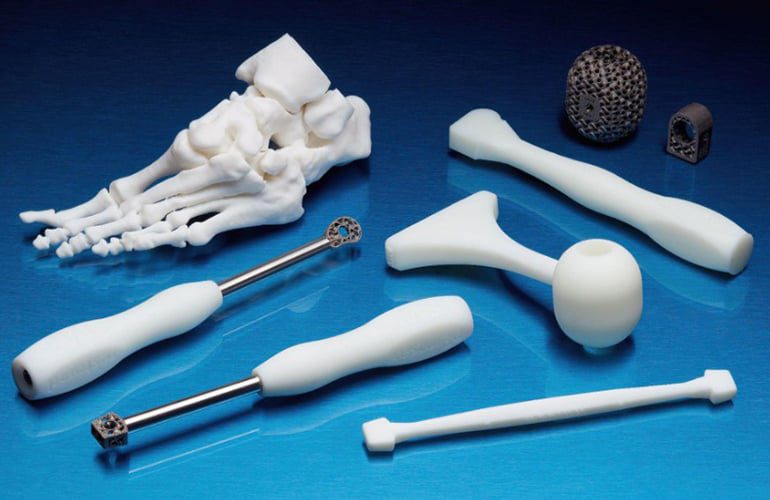
The medical field has been growing quickly in recent years, especially in the use of technology to improve the lives of patients. is now having a significant impact is 3D printing, which was first developed in 1981 but has seen recent breakthroughs.
Through 3D printing, experts can create personalized implants and prosthetics, presenting new opportunities for orthopedic care.
Conventional orthopedic implants have had limitations.
Surgeons have traditionally faced limitations when choosing orthopedic implants, such as having only a few implant sizes available for procedures like knee replacements. Research has suggested that a surgeon should even consider factors like the patient's shoe size.
However, regardless of these factors, surgeons had to select from pre-defined implant sizes based on scan and imaging tests.
The same is true for shoulder implants. Although technology has improved, even when surgeons utilized 3D planning,exact matches were as low as 72% in some cases.
How 3D Printing is Changing Orthopedic Implants
When 3D printing became popular, it was initially used for creating various items, leading to the interest of medical professionals.
Today, 3D printing is utilized for a wide range of medical items, including devices and testing products for diagnostics, and now has a significant impact on orthopedic implants.
In addition, 3D printing is beginning to have a major impact in orthopedic implants.
One studyindicated that researchers are now able to utilize the technology in tissue engineering.It's important to note that 3D printers can work with various materials, making this technology a crucial discovery for the medical industry. important development for the medical field.
Previously, orthopedic implants were produced based on standard requirements, but 3D printing has changed this, enabling personalized care.
It's important to understand how this process functions, especially if you are considering orthopedic surgery overseas.Having knowledge of the capabilities of 3D printing technology will provide better understanding and insight into the procedure.
The process begins with an analysis of the patient's body, allowing for the custom creation of highly accurate personalized implants.
Different imaging methods can be used to help the technician understand how to design the implant. Each implant is customized for the patient using specialized 3D modeling programs.
The specific imaging technology they use depends on factors such as the area and complexity of the implant, and the facility for the surgery.
Ultrasound, MRI, CT scans, and X-rays are all useful in guiding the technician to create the 3D model of the implant. In most cases, a combination of these technologies is used for a more complete understanding of how the implant should be shaped.
After creating the 3D model, the next step is to transfer it to a 3D printer. Then, they select the materials for printing the implant. In most cases, metal is the primary material used. metal is the main material that the technician will use. It’s a strong material that also lasts long.
Metal has been the standard for many types of implants over the years. Even though 3D printers continue to use this material, the benefit here is that the implant is created specifically for you, providing a more exact fit.
The final step is the surgical procedure, which involves general anesthesia. The surgeon removes the damaged tissue before placing the implant. Although the procedure remains invasive, a better fit may make it easier for the surgeon to ensure the implant is properly placed.
A more precise fit usually means less discomfort compared to using a universal implant. However, your body still needs to go through the healing process. You can expect pain, but your surgeon will usually prescribe medication to help you deal with these symptoms.
Currently, there is a significant focus on 3D bioprinting, which uses tissues from your body to print new parts. Research suggests that 3D bioprinting could change how orthopedic surgeons address problems like cartilage deterioration and bone injuries in the future.
Conclusion
Advances in 3D printing technology have made it possible to create custom orthopedic implants with better success rates. Although metal is still widely used in these techniques, the ability to create interesting designs allows the implants to fit better in the patient’s body.